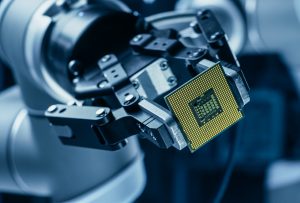
Residual Gas Analysis for Hermetically Sealed Devices
To be hermetically sealed essentially means to be airtight so that nothing can come in or get out (i.e., gas, moisture, liquid, etc.).
Home » Unlocking the Power of Automated Test Equipment (ATE) and Customized Solutions
Automated Test Equipment (ATE) systems are carefully designed to test a wide range of semiconductor devices, including microprocessors, graphic processors, networking switches, cloud computing processors, AI devices, RF devices, and power management components. The ATE system uses precise instruments to apply stimuli to the semiconductor device and measure its response. This verification ensures that the device meets the specifications outlined in the test program. Initial characterization takes place during development to confirm specifications and margins in different conditions. In production, ongoing reliability monitors are periodically conducted throughout the device’s lifetime to ensure consistent performance and durability.
Automated wafer tests performed with a production wafer prober typically involve whole wafers, while engineering mode allows testing partial wafers by aligning each die separately on a manual wafer prober system. ATE systems play a crucial role in testing semiconductor dies on a wafer to identify a known good die (KGD).
These tests, ranging from simple IV or CV tests to more complex evaluations, including DC parameters, structural assessments, and functional tests, aim to ensure the device is free of manufacturing defects. With semiconductor devices now containing billions of transistors, comprehensive functionality testing becomes increasingly challenging, prompting a rise in the adoption of system-level tests for complex devices. ATE systems are frequently utilized in failure analysis, capable of identifying failing tests and using shmoo plots to pinpoint failures within specific operating ranges of voltage, frequency, and timing. The Automated Test Equipment includes tools for recording test times, facilitating analysis to identify areas where the test time is longer than expected. As production data is collected and analyzed, sometimes a particular test can be eliminated, or allow investigation of specific tests to focus on optimization.
An engineer begins testing by creating a detailed plan that outlines the procedure for each specific test. They then program the ATE operating system to generate the corresponding test program. Modern practices often use table formats to specify the test flow and parameters like timing, voltage, current, and test patterns. Electronic Design Automation (EDA) tools from companies like Cadence, Synopsys, and Siemens help generate test patterns. The complexity of test program generation requires programming skills in languages like C++, Visual Basic, Java, and C# to create custom test methods not in the standard ATE system library. Python is also commonly used for processing data collected during the ATE test.
EAG has a variety of Automated Test Equipment (ATE) configurations for Advantest 93K, Teradyne UltraFlex, Teradyne J750, Teradyne IP750, Eagle ETS364, Eagle ETS88, Chroma 3650, Chroma 3680, and Credence Quartet. In our ATE systems, we perform RF testing up to 12GHz, and the power range is adjustable, reaching up to 500V for certain RF tests. Our capabilities include testing high-speed asynchronous interfaces like PAM4 224G SERDES, using Multilane instruments capable of handling speeds up to 112G. Additionally, EAG provides burn-in and High-Temperature Operating Life (HTOL) capabilities for a wide range of semiconductor devices, including those with high pin count, high power, and lower performance.
Teradyne and Advantest both design and manufacture state-of-the-art ATE systems that contain high-speed digital I/operating systems, high pin count, and high power as well as RF and analog functions. Choosing the right ATE system requires aligning it with device test specifications, checking availability, and considering the test engineering expertise. Gage R & R is commonly used to validate the reliability and consistency of new test programs, ensuring repeatable results and reproducibility across different ATE systems, load boards, and probe cards.
As emerging technology nodes incorporate more transistors, enhanced functionality, high-speed IOs, and operate at higher power levels, they pose challenges such as increased pin counts, necessitating precise channel configurations on testers and functioning at elevated frequencies. This complexity adds a layer of challenge in selecting suitable testers and developing functional test programs. Notably, for automotive, aerospace, and defense devices, there’s a growing demand for a broader temperature range, typically ranging from -55°C to +150°C, to meet stringent test and reliability requirements.
EAG provides tailored ATE test solutions to meet the unique needs of clients. Our services include 24-hour access to test equipment, whether onsite or remotely, utilizing electronic travelers for seamless tracking. Our systems are adaptable for operation in private, enhanced security, and clean room environments. In cases where automated tests are not feasible, we offer alternative solutions such as system-level and bench tests. Contact EAG today.
To be hermetically sealed essentially means to be airtight so that nothing can come in or get out (i.e., gas, moisture, liquid, etc.).
FA plays a critical role in product development and improvement. During this live Ask the Expert event, we will answer pre-submitted questions from our audience about electronic device failure analysis.
February 12, 2025
During this live Ask the Expert event, we will answer pre-submitted questions from our audience regarding Silicon Carbide for High Powered Electronics. EAG Laboratories has a vast depth of experience analyzing silicon carbide using both bulk and spatially resolved analytic techniques and is the world-leading materials characterization and engineering resource for semiconductor testing.
The elemental purity of boron carbide can be measured using several methods offered by Eurofins EAG Laboratories
To enable certain features and improve your experience with us, this site stores cookies on your computer. Please click Continue to provide your authorization and permanently remove this message.
To find out more, please see our privacy policy.