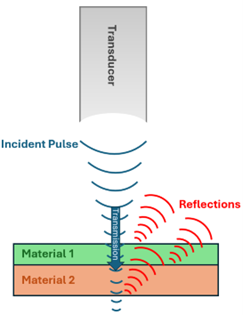
Complementary Techniques: X-Ray & SAM
Complementary Techniques: X-Ray & SAM X-ray imaging is a great non-destructive technique that is used in many industries to help visualize internal construction. Scanning acoustic microscopy (SAM) is another non-destructive