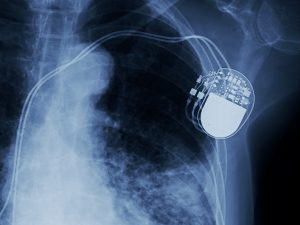
Failure Analysis of Medical Device Electronics
As medical devices become more complex, there are many more opportunities for things to go awry. Identifying, diagnosing, and remedying failures becomes dramatically more challenging. We can help.
Failure Analysis in Aerospace Advancements
Home » Failure Analysis in Aerospace Advancement
In 1903, the Wright brothers made history and presented the first aircraft capable of sustaining powered flight. Flight was made possible by the breakthrough invention of pilot operated wing-warping, crafted carefully by detailed research and incredible engineering.1 This success thus resulted in the birth of the aerospace industry.
From 1903 to modern times, the industry has expanded into commercial airplanes, spacecrafts, satellites, missiles and more, consequentially resulting in increasingly more complex electronic systems. Although these technological advancements are welcomed and necessary in today’s climate, the complexities that come with development present a variety of new problems including quality and safety standards.
EAG can assist with your failure analysis needs.
In the aerospace industry, electronics are subjected to extreme environmental variables such as wide and sudden swings in temperature, strong vibrations, lightning strikes, a multitude of forces acting in different directions simultaneously, severe pressure differentials, moisture intrusion, and ionizing radiation. This can lead to potential issues with control systems, impair aircraft sensors, hinder communication systems, and even compromise structural integrity. To help solve these problems, EAG’s failure analysis experts use advanced analytical tools and proven methodologies to achieve high quality results and reliable engineering assessment.
Some examples of techniques and tools we can use:
EAG is a certified partner (ISO 9001:2015, ISO 17025, ITAR compliant, MIL standards compliant) and offers services to assist with the innovation of new high-performance electronics, collaborate during the iterative efforts of increasing long term reliability, and when necessary, perform comprehensive investigations to identify elusive failure mechanisms. We support innovation at every phase of the product cycle.
Our engineers are knowledgeable and experienced in today’s advanced technologies and are well equipped to help assist in your investigative needs.
1 Culick, F. E. C. (2003). The Wright brothers: first aeronautical engineers and test pilots. AIAA journal, 41(6), 985-1006.
As medical devices become more complex, there are many more opportunities for things to go awry. Identifying, diagnosing, and remedying failures becomes dramatically more challenging. We can help.
Contamination control and defect reduction are critical issues in the manufacturing process of compound semiconductor devices which can impact the performance of the end product. We can provide valuable insights to identify contaminants and characterize materials throughout the product lifecycle.
Damage caused by ESD is one of the primary failure mechanisms for integrated circuits. Testing susceptibility to ESD events is crucial in the success of electronic devices and is essential for the qualification process.
During this live Ask the Expert event, we will answer pre-submitted questions from our audience regarding materials characterization and failure analysis using Plasma FIB (PFIB). PFIB extends conventional DualBeam (DB) capabilities to nearly mm scale without the use of Gallium.
To enable certain features and improve your experience with us, this site stores cookies on your computer. Please click Continue to provide your authorization and permanently remove this message.
To find out more, please see our privacy policy.