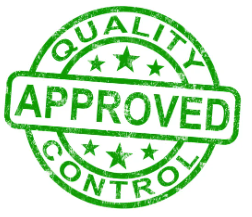
From Certifications To Customer Audits, Quality Matters
EAG Laboratories pursues quality in all aspects of our work for customers. ISO certifications and ongoing audits serves many market sectors.
Home » The Birth of PCOR-SIMS for Silicon Germanium (SiGe) Devices
In the mid-1990’s the development of higher frequency Silicon Germanium devices (SiGe) gained momentum to address the need for increased performance in wireless systems. This demand was driven by the need for low-cost, and lightweight personal communications devices such as cellular phones and laptops, as well as other entertainment and information technologies which used wireless communication. Silicon Germanium provided easier integration to existing lower cost Si integrated circuits.
Developing Silicon Germanium (SiGe) devices was intricate and consuming, as it required various iterations, which led our customers to ask us to develop a method for acquiring accurate profiles for both dopants and matrix elements in Silicon Germanium (SiGe) materials. The objective was to accelerate development by bringing high accuracy characterization into the R&D and failure analysis cycle.
As with any innovation, or a change in the status quo, there were naysayers – or those who poked holes at what could be possible. It was commonly assumed that Secondary Ion Mass Spectrometry (SIMS) could not quantify matrix-level concentrations with sufficient accuracy, and calibrating dopant intensities continuously, with respect to varying matrix composition, as it would would be prohibitively time consuming. The naysayers however, helped a great deal by motivating the team to focus on perfecting the methodology of the technique to make it into what it is today. PCOR-SIMSSM, or Point-by-Point CORrected-SIMS, was birthed out of this need for a deeper level of accuracy.
PCOR-SIMSSM is a technique that can measure layer thickness, composition, and doping profiles more accurately than a regular SIMS analysis, where the calibration is made at every data point with respect to change in the matrix composition. With the creation of the PCOR-SIMSSM analysis, EAG Laboratories was now able to provide more useful information due to better accuracy and reduced error. This in turn saved our customers’ time, money, and resources to solve a problem they might not have been able to solve on their own as quickly.
The development of the PCOR-SIMSSM method required the testing of a variety of samples, acquired in collaboration with Academia and the National Institute of Standards & Technology (NIST), and analyses by other techniques such as Rutherford Backscattering Spectrometry (RBS), Nuclear Reaction Analysis (NRA), Transmission Electron Microscopy (TEM), X-ray Photoelectron Spectroscopy (XPS), etc. These analyses formed the basis for the empirical relationships between intensity and concentration that are the underpinnings of the PCOR-SIMSSM methodology.
As with anything, PCOR-SIMSSM must constantly adapt and evolve as more complex materials are developed. This technique continues to prove to be a valuable resource to EAG customers to achieve a more accurate analysis and to provide the data they need to create sophisticated products efficiently. We would love to partner with you to help with your PCOR-SIMSSM related projects. Contact us today to learn more about how to utilize our proprietary PCOR-SIMSSM technique.
EAG Laboratories pursues quality in all aspects of our work for customers. ISO certifications and ongoing audits serves many market sectors.
During this Ask the Expert webinar, our team of battery materials experts will address your pre-submitted questions during the event, as well as present about our new battery lab’s capabilities.
Product liability cases have many complexities and challenges and require top-notch legal services. Navigating the intricate details of these cases requires not only legal insight but also specialized expertise in various technical and regulatory domains.
Women in STEM Career Fair Eurofins EAG Laboratories is excited to host a Women in STEM Career Fair on March 31st from 3 PM – 6 PM ET! We’re looking
To enable certain features and improve your experience with us, this site stores cookies on your computer. Please click Continue to provide your authorization and permanently remove this message.
To find out more, please see our privacy policy.