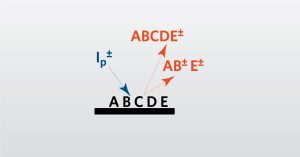
TOF-SIMS Webinar
In this webinar we introduce TOF-SIMS which is a surface analysis technique used to investigate the extreme surfaces of samples.
Home » Surface Analysis on 3D Printed Titanium
The additive manufacturing (AM) market, also known as 3D printing, continues to grow and expand into a wider range of applications within high technology industries. AM enables the ability to create more highly customizable designs, opening this market to new opportunities. The high demands on product quality in these sectors have substantiated the need for advanced materials characterization, often according to standards.
For 3D printed products, X-ray Photoelectron Spectroscopy (XPS) can provide composition and bonding information for the top 5-10nm sample surfaces. Oftentimes, surface contamination/oxide thickness would affect the appearance (as well as performance when applicable) of the material, and XPS could help identify the source and/or cause. If the contaminant and/or oxide layer is thicker than 5-10nm, XPS depth profile analysis could be performed (down to 1um) in studying the penetration depth of contamination and/or oxide layer.
In studying the uniformity of surface composition, XPS survey analysis was first carried out at multiple sample locations. Image below identifies three example locations, two at the edge of the sample and one in the middle.
XPS survey results showed that the composition for all three areas were similar, which all three areas were composed predominantly of silicone with only very trace levels of Ti, though Ti was expected to the major component of the substrate material.
In addition, representative high-resolution elemental spectra showed similar bonding chemistry at the three locations. The binding energies of C and Si were likely associated with silicone, based on the sample stoichiometry. Titanium was found as a combination of TiO2, Ti(Al)OxNy and Ti(Al)Nx. Aluminum was found as Al3+ (possibly as AlOx), while nitrogen was found as a combination of organic N (C-Nx) and nitride.
A light Ar cluster sputter on the sample surface was then applied, with the attempt to remove surface organic contaminants and loosely bounded species. Data below showed the Ti, Al and N concentration increased substantially after the light Ar cluster sputter, indicating the Ar cluster sputter did help removed some surface contaminant.
High-resolution spectra showed oxidized Al and Ti species were still present on the sample surface, indicating the gentle Ar cluster sputtering did not damage the sample surface bonding chemistry. After the sputter, higher composition of Ti(Al)OxNy and Ti(Al)Nx were detected, along with a lower binding energy component of Al that could be attributed to Al0 and/or Al-alloy. This is an indication for the formation of a thin oxide layer on the sample surface. In addition, trace levels of V0 and/or V-alloy were also detected. The presence of trace levels of Cu0/CuI and Zn could either be part of the ink composition and/or contamination during the 3D printing process.
Though the level of silicone was reduced considerably after the Ar cluster sputter, a substantial amount of silicone was still detected on the sample surface. To confirm whether silicone was a surface contaminant (if so, how thick the silicone layer is), or whether it was indeed part of the 3D printing ink, a monoatomic Ar ion sputter depth profile was carried out.
Depth profile analysis indicated high levels of organic species (including silicone) were detected throughout the 1µm (SiO2 equivalent) profiling depth. Further analysis is needed to check the penetration depth of the silicone and organic species. Elemental scans throughout the depth profile indicated Ti was likely present as Ti(Al)OxNy and/or Ti(Al)Nx, while the presence of TixVyAlz could also be possible due to the presence of Al- and V- alloy. Aluminum was found primarily as Al3+, likely as AlOx as indicated in the XRD results.
XPS surface analysis indicated the surface of the 3D printed sample was composed primarily of silicone, with only trace levels of metallic species being detected. Depth profile analysis showed there were high levels of carbonaceous species on the top 1um of the sample surface. XPS is good for characterizing the sample surface for composition and bonding information. Aside from hydrogen and helium, anything that is vacuum compatible could be analyzed by XPS, with a detection limit as low as 0.1 atomic %.
At Eurofins EAG, our technical experts have many years of experience with surface analysis on a wide range of materials. Contact us today to learn how we can help you on your next 3D printed project.
In this webinar we introduce TOF-SIMS which is a surface analysis technique used to investigate the extreme surfaces of samples.
In this webinar we introduce X-ray Diffraction (XRD) which is a analytical technique for the examination of crystalline materials.
Lithium-ion batteries provide high energy density mobile power but come with three challenges: performance, safety and battery life.
In this webinar we introduce analytical techniques used by EAG for surface analysis – XPS, Auger and TOF-SIMS
To enable certain features and improve your experience with us, this site stores cookies on your computer. Please click Continue to provide your authorization and permanently remove this message.
To find out more, please see our privacy policy.