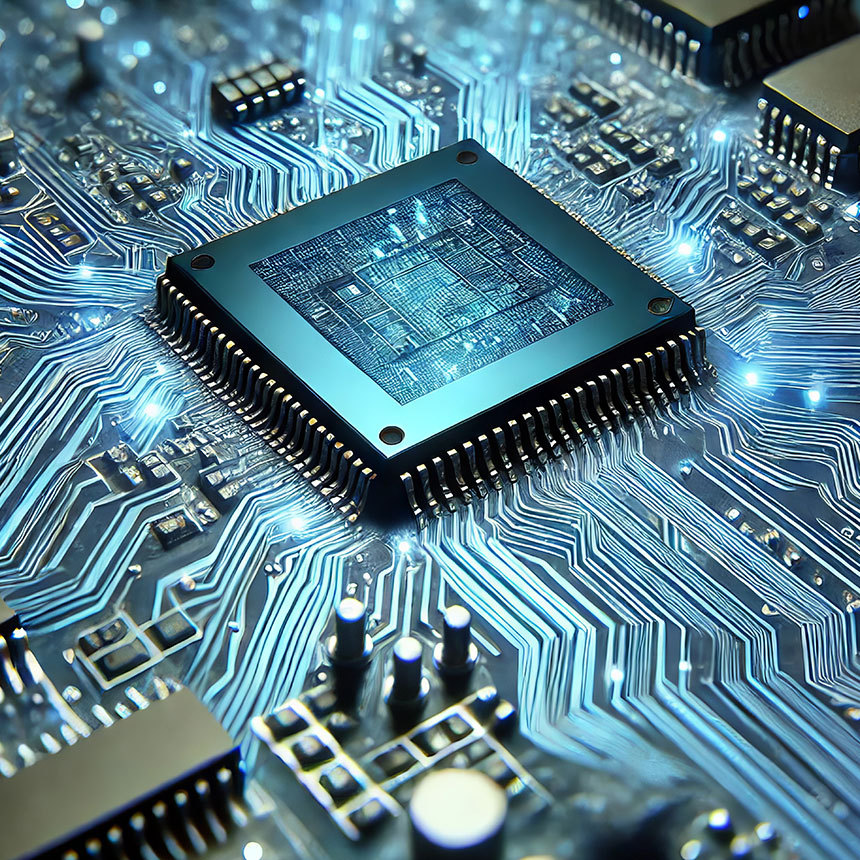
Determine Electrical Properties Using Electrical AFM
Electrical AFM can measure the electrical/electromechanical properties of various functional materials and samples. This helps distinguish between conductive and nonconductive areas or polar and nonpolar regions of a device.