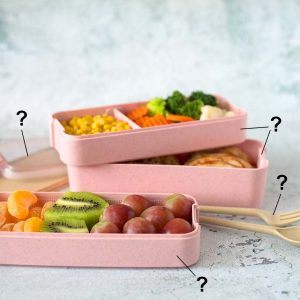
FTIR and Raman – Composition and Contamination Analysis
FTIR and Raman are spectroscopy techniques that provide molecular information from various types of materials.
Home » Ion-Exchanged Glass: Smart Technology for Smartphones
In a 2015 study by Deloitte, it was found that Americans collectively check their smartphones upwards of 8 billion times per day – and usually while doing something else (this number is now likely higher).1 This provides a lot of opportunities for consumers to drop their phones and possibly break the glass screen. Luckily, Ion-exchanged glass, the best-known example of which is Gorilla Glass™, was accidentally discovered in 1953 by a Corning Glass Works research chemist who mistakenly heated a piece of FotoForm glass to a temperature of 900° C and noticed that it bounced on the floor, instead of shattering, when he dropped it. This serendipitous invention of the first chemically strengthened glass ceramic would evolve into the material that today protects billions of smartphones, tablets, and laptops from unwanted damage.2
Ion-exchanged glass is a type of glass that has been treated to enhance its strength and durability by exchanging ions within the glass structure. The process involves immersing the glass in a
molten salt bath and exchanging sodium ions in the glass surface with larger ions such as potassium or silver in the salt bath. This process is known as ion exchange, and it creates a layer of compressed glass that is stronger and more resistant to damage.
This type of glass is used in a variety of applications where strength, durability, and resistance to damage are important. It is commonly used in the manufacturing of touchscreens, glass for smartphones, tablets, and other electronic devices. It is also used in the production of windows for buildings, automobiles, and aircraft. Additionally, ion-exchanged glass is used in the manufacturing of laboratory glassware, as it is more resistant to thermal shock and chemical corrosion than standard glass.
The process of making ion-exchanged glass involves several steps. First, the glass must be prepped by cleaning the glass and cutting it to the desired shape and size. Next is the Ion Exchange Bath where the glass is immersed in a molten salt bath that contains ions that are larger than the sodium ions in the glass. The glass and the salt bath are then heated to a specific temperature and held for a certain amount of time to allow the ion exchange to occur. Lastly, the glass is cooled slowly to prevent thermal shock and washed to remove any residual salt.
The depth of the region of ion exchange in ion-exchanged glass can vary depending on several factors, including the type of glass, the ion species used for the exchange, and the conditions of the ion exchange process. In general, the depth of the ion-exchanged region is typically on the order of a micrometer (μm) to tens of micrometers.
It is worth noting that the depth of the ion-exchanged region is not the only important factor in determining the properties of ion-exchanged glass. Other factors such as the type and concentration of the exchanged ions, as well as the initial glass composition, also play significant roles in determining the ultimate properties of the glass.
Eurofins EAG scientists can help determine the depth of the ion-exchanged region through various instrumental techniques and objective-specific, validated, methods. Purity Analysis, using a range of techniques, can be performed to determine if unintentional trace contaminants in the glass are affecting its material properties. Laser Ablation-ICP-MS can determine how deep the ion exchange region went into the glass. Secondary Ion Mass Spectrometry (SIMS) can also characterize the depth of the ion exchange to see if goals were achieved during the molten salt bath process, while X-ray Fluorescence (XRF) can assist with determining the concentrations of major elements though the diffusion profile of the ion exchange region and into the unaltered region in the middle of the glass (with chemical etching steps).
For over 40 years, Eurofins EAG has been involved in the entire value chain of glass, from raw starting materials to final products. Our scientists investigate the composition and quality of raw materials and production glass and provide research support to glass factories during product development, process optimization, glass tank wear-out studies, verification tests, and failure analysis investigations. In the field of surface modification, delamination, and corrosion of coatings, Eurofins EAG has unmatched expertise.
Contact Us today to learn more about how we can partner to meet your glass-related product needs.
1Eadicicco, L. (2015, December 15). Americans Check Their Phones 8 Billion Times a Day. TIME Magazine.
2Rohrig, B. (2015, April/May). Smartphones Smart Chemistry. ChemMatters, pp. 10-12.
FTIR and Raman are spectroscopy techniques that provide molecular information from various types of materials.
Unwanted chemical impurities can be problematic. GDMS is a powerful full survey analysis tool for chemical purity evaluations.
Biocompatibility assessments are a battery of tests performed to evaluate a product, medical device, or other material for the risk of biological hazards.
In this webinar we introduce EAG Laboratories advances in Materials and Surfaces Characterization of Medical Devices
To enable certain features and improve your experience with us, this site stores cookies on your computer. Please click Continue to provide your authorization and permanently remove this message.
To find out more, please see our privacy policy.