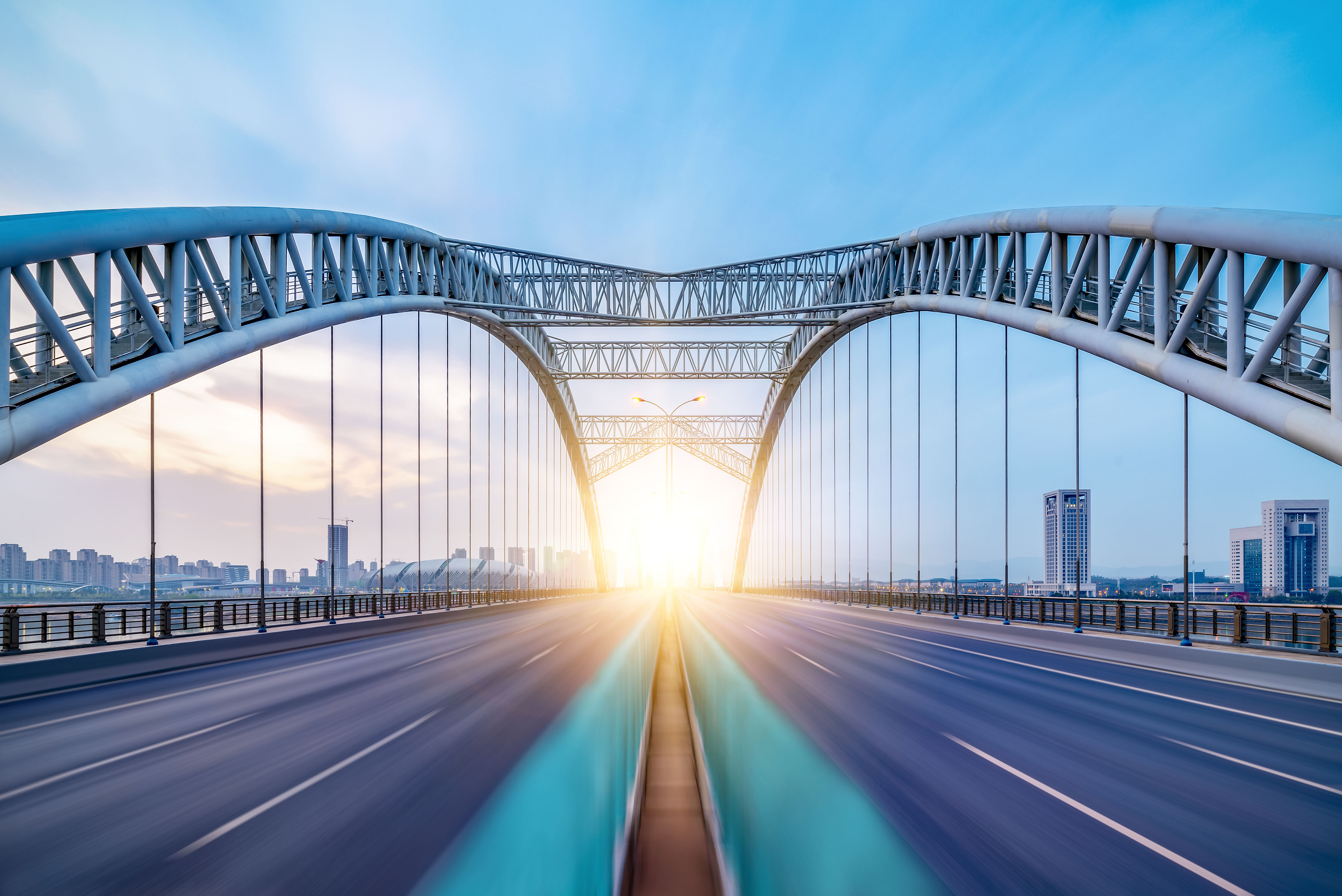
When Metal Fails: How Metallurgy Helps Us Understand Bridge Collapses
When Metal Fails: How Metallurgy Helps Us Understand Bridge Collapses INTRODUCTION Bridges are marvels of human engineering. Many bridges are even famous landmarks. Despite their impressive appearance, some bridges tragically