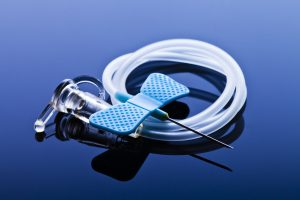
The Vital Role of Failure Analysis in Medical Device Electronics
Failure analysis plays a crucial role in the development and maintenance of medical device electronics.
Home » Accurate Composition and Quantification of Materials – RBS
What is the gold foil experiment? Think back to high school chemistry! Atoms were originally thought to be uniformly solid balls until 1911 when Lord Ernest Rutherford designed an experiment to prove whether or not an atom was truly solid. To simplify the explanation of this experiment, visualize little bb gun pellets (as tiny, positively charged particles) being shot directly at a thin layer of gold foil. Most of these particles went right through the gold as expected. However, some of the particles ricocheted back at various angles. From this, it was determined that the atom’s mass was concentrated in a tiny nucleus while the nearly mass-less electrons made up the volume around it. The real experiment used helium nuclei, also known as α (alpha) particles, not mini bb gun pellets! The conclusion that the positively charged nucleus was concentrated in a small volume was in strong contrast to earlier models that had proposed that the positive and negative charges in an atom were uniformly distributed.
Based on Rutherford’s gold experiment, Rutherford Backscattering Spectrometry (RBS) was born. The measurement of the energy of
ions which backscatter after colliding with a sample’s surface can be used to determine the atomic composition and the elemental concentrations in a sample. RBS is the one technique where we can really say that the composition and concentration are accurately determined for thin films.
RBS is unique in that it allows quantification to be done without the use of reference or calibration standards. Most other techniques use a correction factor or need references of known composition to determine concentrations. With this capability, RBS is sometimes used to create calibration standards for other techniques, such as Secondary Ion Mass Spectrometry (SIMS).
In addition, since RBS provides a macroscopic and quantitative measurement of the film composition, it is a good starting point as well as complementary technique to more surface sensitive techniques such as SIMS and X-ray Photoelectron Spectroscopy (XPS), wherein a more complete picture of the structure and properties can be obtained.
From product development to failure analysis, RBS is a very valuable technique.
In production process control, RBS can help to ensure and maintain consistency in film thickness and composition over longer periods of time. It can help with accuracy and precision for deposition processes. It can translate process parameters into concrete numbers. RBS can also help to fine tune the desired properties of a film in conjunction with process modifications. For failure analysis projects, RBS can help diagnose problems such as the amount of film being used or applied on a surface.
The hydrogen content of a film can potentially affect the properties and performance of a product. During production processes, there may be a need for a specific amount of hydrogen or none at all. RBS can help with hydrogen measurements on materials such as carbon films, low k dielectrics and other films on semiconductors, including dielectric films.
Eurofins EAG Laboratories is one of the very few worldwide to offer RBS in a commercial lab environment. With our multitude of techniques, we have the resources to use RBS as a standalone measurement or in conjunction with other tools. Our decades of experience and breadth of services allow us to work closely with our clients to tailor an analytical plan to their needs.
Contact us today to learn how we can help you on your next project.
Failure analysis plays a crucial role in the development and maintenance of medical device electronics.
In this webinar we introduce the Testing of High Speed I/O to validate the devices from characterization to production
In this webinar we introduce Fractography which is a failure analysis evaluation technique when components fracture
In our interconnected and changing world, it is important to know how to respond to potential electronic system failures.
To enable certain features and improve your experience with us, this site stores cookies on your computer. Please click Continue to provide your authorization and permanently remove this message.
To find out more, please see our privacy policy.